Les gréements de forage d’exploration sont la prochaine frontière de l’automatisation minière, mais quelle innovation émerge et se produit-elle assez rapidement?
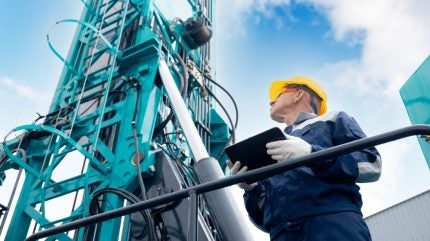
L’exploration minérale est souvent considérée comme un processus rudimentaire; L’une des géosciences hardcore, avec les prospecteurs qui se penchent sur des cartes et collectaient des échantillons de noyau de roche en utilisant une technologie de forage qui, pour la plupart, est toujours contrôlée manuellement.
En revanche, du côté de la production, un équipement de forage autonome est désormais standard, allant de la télécommande, du télé-rectinement et semi à complètement autonome.
La technologie de forage d’exploration est donc considérée comme mûre pour l’innovation, avec de nombreuses entreprises – des start-ups aux piliers – en lice pour apporter une automatisation accrue sur le marché. Les avantages, disent-ils, sont une myriade. Les plates-formes d’exploration automatisées peuvent améliorer la sécurité en éliminant les personnes des situations à haut risque et en nécessitant moins d’intervention de foreuse, en aidant à faciliter les pénuries aiguës de main-d’œuvre dans le secteur. L’automatisation peut également réduire les coûts globaux, étant donné que les salaires, qui peuvent coûter de 10 000 à 50 000 $ par jour, sont l’une des principales dépenses qui se sont produites pendant les campagnes de forage, en plus des délais potentiellement courtois.
De plus, à mesure que la transition énergétique se déroule, la demande de nouvelles découvertes minérales devrait augmenter, l’agence internationale de l’énergie prédisant 40 fois plus lithium Et sept fois plus de terres rares potentiellement nécessaires d’ici 2040 – une prévision à peine compatible avec les 16,5 ans moyens nécessaires pour identifier et opérationnaliser une nouvelle mine.
La technologie est donc accueillie par les investisseurs et les prospecteurs. «Tout ce qui implique l’automatisation est généralement une opportunité d’interférence minimale, moins de risques, une efficacité élevée et moins de production en carbone – qui sont tous alignés sur les objectifs durables de l’ONU et le net zéro», explique Thomas Balogun, partenaire d’investissement chez Echo EXPOSTS.
«Vous ne dites jamais non à ce type de progrès technologiques», ajoute Yannis Tsitos, président du comité minier de Blue Lagoon Resources, qui développe le projet Dome Mountain Gold en Colombie-Britannique, au Canada.
Qu’est-ce que les OEM attendaient?
Le principal problème identifié par les fabricants d’équipements d’origine (OEM) est que l’automatisation de la manipulation des tiges pour une plate-forme d’exploration est considérablement plus complexe que pour un forage de production.
L’exploration nécessite du forage à des profondeurs beaucoup plus importantes que ce dernier, ce qui signifie qu’il s’agit d’un processus plus technique. L’exercice nécessite généralement l’accès à plusieurs tiges de forage de l’extérieur de la zone du mât, augmentant le risque pour l’opérateur. Les systèmes de manutention des tiges doivent être «enseignés» à partir à partir d’un nouveau poste pour chaque trou, explique James Burris, directeur marketing chez Drilling Equipment and Service Provider Banyear, qui opère dans le secteur depuis 150 ans.
L’entreprise passe ses plates-formes de la manipulation manuelle à plus autonome et «focalisée de la gestion du forage» depuis 2016, lorsqu’il a lancé le LF160 avec une manipulation de tige mains libres, qui a atténué la manipulation de la tige de forage lourde dans la zone du mât. C’était le «fruit à faible suspension», explique que le chef de produit Zachary Strauss. L’étape suivante a été l’automatisation de la manipulation des tubes intérieurs, introduite avec le LF160i. Une fois plein de noyau rocheux, et surtout si le forage à un angle abrupte, le tube intérieur peut être difficile et risqué d’extraire manuellement, mais l’automatisation délivre désormais horizontalement les tubes sur le plateau central pour le démontage et l’élimination des échantillons.
En s’appuyant sur cela, la société teste désormais un groupe de contrôle digéré pour le LF160i au Chili et en Australie, qui devrait être officiellement lancé à la fin de cette année. Les leviers actionnés hydrauliques sont omis et le panneau passe de l’acier lourd aux écrans numériques et aux joysticks. Il ne nécessite aucune intervention de l’assistant du foreur pour aligner et faire le vélo des tiges ou connecter les bougies de levage lors de l’exploitation du chargeur. De plus, certaines opérations fastidieuses, telles que le positionnement de la tête de forage pour la manipulation des tiges, peuvent être automatisées.
Les mêmes avancées sont faites pour les plates-formes souterraines, mais les contraintes d’espace rendent le processus plus délicat.
Strauss dit que l’automatisation dans le forage d’exploration ne concerne pas les «grands sauts», mais les «changements incrémentiels qui nous mènent là où nous essayons d’aller», qui est finalement d’avoir un opérateur de forage qui mène plusieurs plates-formes à la fois, peut-être à distance, en utilisant des données collectées à la machine pour un dépistage plus rapide.
«Je crois que l’industrie en est capable aujourd’hui, mais les conditions de forage détermineraient la viabilité ou si elle était économiquement avantageuse», dit-il. Il y a des avantages et des inconvénients, ajoute-t-il; Le fonctionnement manuel nécessite plus d’attention de l’opérateur, induisant la fatigue et les erreurs potentielles, mais certaines étapes peuvent prendre plus de temps lorsqu’elles sont automatisées car elles nécessitent du vélo grâce à plus de contrôles de sécurité.
Les clients surveilleront de près les avantages économiques. Par exemple, le géologue professionnel Eric Saderholm, directeur général de l’exploration et co-fondateur d’American Pacific Mining Corp, un développeur de métaux précieux et de base dont l’automatisation n’est peut-être pas une option financière pour les programmes d’exploration régionale.
En effet
«Ce n’est qu’alors que cela deviendra un élément de ligne budgétaire», dit-il.
Cependant, la plupart des OEM d’équipement de forage sont sur ce chemin. Il y a deux ans, le fabricant suédois EPIROC a collaboré avec le fournisseur de services de forage d’exploration Ausdrill pour développer une plate-forme avec une manche entièrement automatisée, y compris une automatisation de séquence pour les processus. Les entreprises ont déclaré qu’il était impératif de s’assurer que le système de gestionnaire de tiges était plus rapide que les opérateurs «sinon ils continueraient simplement à faire le travail manuellement».
Perturbateurs technologiques et conservatisme de l’industrie
Avec les opérateurs opérateurs, les entreprises moins connues, espionnent une opportunité, sont également axées sur le laser sur la mise en œuvre de l’automatisation dans le forage d’exploration.
Tribe Tech, par exemple, s’est associée à la filiale de Barart Longyear Veracio pour développer ce qu’elle dit être une première plate-forme de foret de circulation inverse autonome, le TTDS GC 700, qui fonctionne sans personnel sur le coussin de forage. La société affirme que la technologie, qui aurait été testée en Australie avec McKay Drilling, peut Améliorer les normes de productivité et de sécurité.
En outre, Durin, basée en Californie, créée il y a un an par Ted Feldmann, prétend construire des plates-formes semi-automatiques à distance exploitées à distance qu’elle prévoit de tester dans des projets d’exploration nord-américains. L’année dernière, il a terminé une séance de financement pré-série avec deux investisseurs.
Balogun pense que les nouveaux entrants auront du mal à garantir le capital dur nécessaire pour vraiment faire décoller les opérations. «C’est trop un pari pour une start-up», dit-il.
La technologie des mines de Xtremex est également ciblée, fondée par des professionnels expérimentés des industries du pétrole et du gaz et des mines. En janvier, il a annoncé son Drill Rig avec un contrôle automatisé et système d’alimentation hybride. Il organisera un essai sur le terrain financé avec Ivanhoe Electric au Santa Cruz Copper Project en Arizona, ciblant des profondeurs allant jusqu’à 2 000 m en jumelant des trous historiques. En vertu de l’accord, Ivanhoe Electric garantit l’exclusivité sur trois plates-formes XMT pour des contrats d’une durée jusqu’à cinq ans.
Pourtant, malgré la technologie d’extraction de Durin et Xtremex ciblant clairement le transfert de technologie secteur du pétrole et du gazTsitos prévoit que ce sont des processus différents.
«Le forage d’exploration nécessite un niveau de précision et d’interprétation des données qui nécessite une surveillance et une perspicacité humaines. Vous essayez de faire en sorte que chaque trou compte pour frapper une ressource potentielle», explique-t-il.
«Cela diffère dans la nature du forage assisté par l’IA pour les champs de pétrole et de gaz, où les trous d’exploration sont plus grands et cibles moins spécifiques pour trouver un potentiel de ressources et de production.»
Innovation inévitable dans le forage autonome
Chris Hall, responsable du développement commercial pour Capital, une société de services miniers basée au Royaume-Uni qui teste une flotte de trou de souffle numérisé (D65) en Tanzanie, dit l’automatisation, ainsi que électrificationest le «Saint Graal» pour l’industrie de l’exploration.
«Il se dirige vers cela [increased automation] Et nous espérons que finalement, la forage pourrait fonctionner avec une intervention limitée du foreur, offrant des améliorations d’efficacité et de sécurité », dit-il.
Les initiés de l’industrie conviennent que l’automatisation complète est inévitable.
«Il est clair que le marché a parlé», explique Burris. «Finalement, l’automatisation complète sera une exigence. Nous en avons été témoins d’un exemple lorsqu’une grande entreprise minière a dicté que tous les entrepreneurs de forage devaient utiliser notre système de manutention LF160 et de tige.»
Cependant, il y a un débat sur le moment, avec les clients plus sceptiques que les développeurs de technologies. Burris dit que des exercices entièrement autonomes sont testés mais estiment qu’ils sont à 3 à 5 ans à partir de la commercialisation. Tsitos convient que, bien que le forage contrôlé par l’IA arrive à l’exploration minière, «la mise en œuvre plus large et l’acceptation de l’industrie peuvent prendre au moins dix à 15 ans».
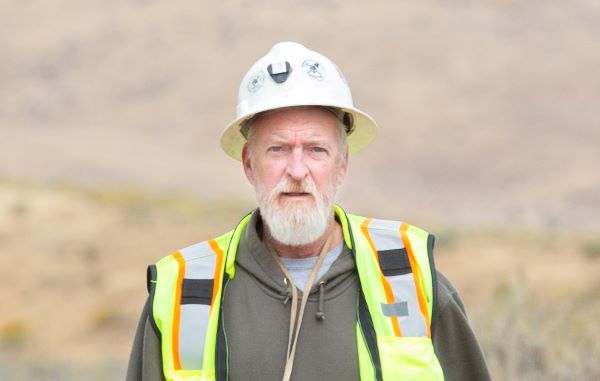
«L’adaptation arrive, mais la rentabilité et la productivité des exercices autonomes dans les paramètres d’exploration à distance sont minimes par rapport aux économies qui peuvent être réalisées dans les mines à grande échelle», ajoute Saderholm, dont la société American Pacific opère dans l’ouest des États-Unis avec des projets en Alaska, au Montana et au Nevada.
«L’exploitation minière évolue à un rythme plus lent que les autres industries», reconnaît-il, «mais une fois que le forage automatisé deviendra une méthode largement prouvée et rentable, les barrages de résistance se briseront et il y aura un flot d’adaptateurs pour la technologie.»
Dans l’état actuel des choses, il est probable que, dans le terme près de médiation, l’industrie aura plus de technologie de forage plus autonome, mais il reste à voir s’il opte pour les experts de longue date de l’industrie ou les perturbateurs technologiques plus récents.
fermer